A monumental problem
The colossal carbon dioxide emitter you’ve probably never heard about (8 minute read)
Welcome to The Turnstone. Here, I help people understand important issues such as Covid-19, climate change and conservation. I send my articles out every Sunday - if you’d like them emailed to you directly, you can sign up to my mailing list.
In the centre of Rome, in a small square which is always busy, stands one of the world’s most remarkable buildings. From the outside, its curved brick and concrete walls aren’t too different from other buildings around the city. The pockmarked columns at its entrance are large, but not an unusual sight in Rome. The inside is decorated with multicoloured marble, but equally beautiful marble can be seen in dozens of Roman churches. It’s only when your eyes rise to the roof can you be sure that this building is like no other you’ve ever seen.
There are no painted frescoes or Baroque gilding. Instead, the dome of the roof is a uniform concrete grey. And it’s massive – 43 metres in height and diameter. The inside of the dome is adorned only with rectangular indentations, known as coffers, in rows of decreasing size as they rise up the dome. At the very top, instead of being closed, the roof is open to the sky. On a wet day, the rain falls. On a fine day, the sun strikes the floor.
From my description of the hole in the roof, you may have realised that the building I’m describing is the Pantheon, which has stood, largely unchanged, for nearly two thousand years. For 1400 years, it was the largest dome in the world, and it remains today the largest dome built of unreinforced concrete.
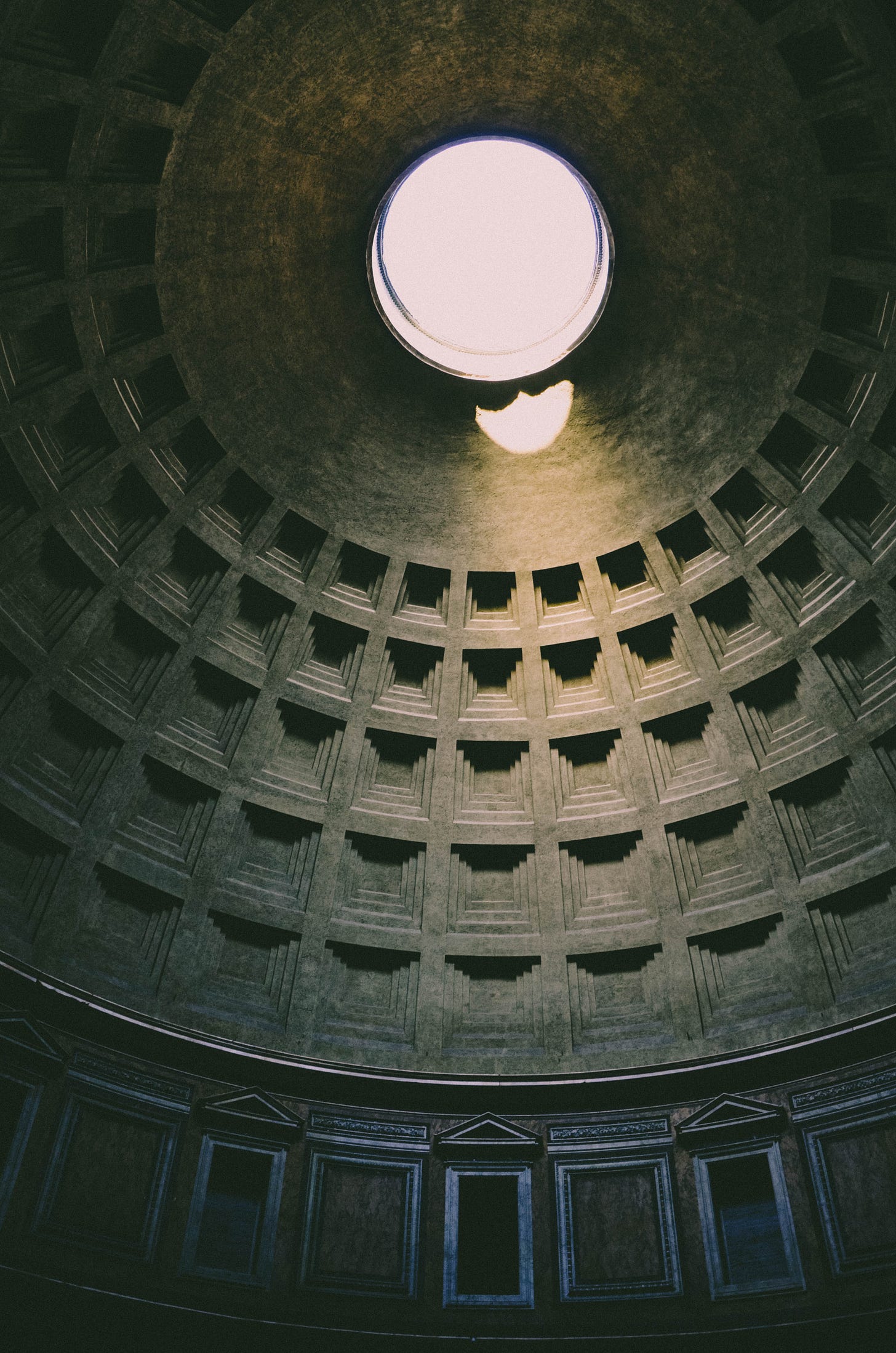
Although there’s no other building quite like the Pantheon, there are many other buildings from ancient Rome, in varying states of preservation, which show the brilliance of Roman engineering. Mighty fortifications still stand too, not just in Rome but in areas which were once the frontier of the Roman empire, such as Britain, Spain and Jordan. Also still in remarkably good condition are fragments of Roman aqueducts, such as the famous Pont du Gard in France.
The durability of these buildings and ruins is partly down to the Roman’s skill with arches, perhaps illustrated most beautifully in the Colosseum (here is a link to a simple video explaining how arches work). But there’s another reason many ancient Roman constructions have survived, and it’s one that you might not think about. The Romans were truly brilliant at using concrete. This humble material was the foundation of Rome – almost literally.
The Romans didn’t invent the first concrete, but they were the first people to use it on a massive scale. Their particular recipe used a chemical called calcium oxide, commonly known as quicklime, ancient volcanic ash and water. It was not a strong as modern concrete, but it was extremely durable over time.
Modern concrete uses a slightly different mixture. Instead of quicklime, modern concrete uses Portland cement, and instead of volcanic ash it uses sand and fine gravel. The principles, however, are the same. The quicklime or Portland cement reacts with the water and slowly hardens. The sand and gravel (or volcanic ash) are largely there to add volume.
However, Roman concrete and modern concrete have crucial differences. While we don’t fully understand the chemistry of the concrete used by the Romans, it was based on the reaction of quicklime and water to produce calcium hydroxide, and then the reaction of calcium hydroxide with carbon dioxide in the air to produce calcium carbonate. Minerals in the ash also contributed to its strength.
In modern concrete, the reaction is different. Portland cement is made up of several different components which react with water and harden. Carbon dioxide is not involved in the hardening process. Each component of the cement hardens at a different rate and to a different degree. The first component to harden contributes little to the strength of concrete, which is why fresh concrete can appear set but you shouldn’t walk on it. Other components are slower to react, but are stronger. The chemical reactions which cause concrete to harden can continue for weeks, months or even years.
Concrete is an incredibly useful building material, but it has a dark secret. It is a huge emitter of carbon dioxide. In fact, if concrete were a country, it would be the third largest emitter after China and the USA. It contributes 8% of global greenhouse gas emissions (although some estimates are lower, at around 4%). In the last 30 years, global cement production has quadrupled, and the increases show no sign of slowing down.
Why does concrete have such a monumental carbon footprint? The reason is the process for manufacturing Portland cement. This process begins with limestone, which is a rock mostly made up of calcium carbonate. Limestone can be formed by coral, by the shells of dead marine creatures falling to the ocean floor or by chemical processes. (If you enjoy chemistry, the simplest explanation of the chemical process I’ve found is in this video showing how stalactites and stalagmites are formed.)
Crushed limestone is mixed with clay or shale (a clay-like rock) and heated to over 1400oC. The crushed limestone releases carbon dioxide to form quicklime, and then the quicklime reacts with the clay or shale to form a compound called clinker, which is a mixture of different chemicals (all of which have long names I’m not going to list here). Another chemical called gypsum is added, the clinker is ground and then you have Portland cement.
Part of concrete’s carbon footprint is the huge quantity of fossil fuel, mostly coal, used to heat millions of tonnes of limestone per year to over 1400oC. But more than half comes from the release of carbon dioxide directly from the super-heated limestone. It’s an intrinsic part of the cement manufacturing process.
It’s hard to imagine concrete without carbon emissions. It’s even harder to imagine the modern world without concrete. And, in the midst of New Zealand’s housing crisis, we can’t solve this problem by building fewer houses. But we can’t ignore concrete’s impact either.
Although concrete’s carbon emissions haven’t received much public attention, there are researchers who are looking for solutions. These solutions come in two broad types – reducing emissions from the cement manufacturing process and using less Portland cement.
Substantially reducing emissions from the cement manufacturing process requires more than just replacing the fossil fuel, but that is a good start. So far, about 30% of the fuel Europe uses in cement manufacture is classed as “alternative fuel”. For the USA, that figure is just under 20%. New Zealand’s Golden Bay cement company claims to be using up to 50% alternative fuel. And a recent study looked at substituting 75% of the coal for an alternative fuel made from waste, and found that it could be done without compromising cement production. However, alternative fuels have some drawbacks. Some of it is derived from waste which was originally made from fossil fuels, such as old tyres, so it’s still contributing to climate change. Hydrogen is also being considered, but if that is produced from fossil fuels, as hydrogen often is, then it is only shifting the problem from one industry to another.
Researchers are also looking for ways to recapture the carbon released from the limestone during heating. In theory, it should be easier to recapture the carbon dioxide released during manufacture than it is to recapture the carbon dioxide released from a power plant, because of the high carbon dioxide levels coming out of cement plant flues. There’s a plant being built in Germany which promises to capture 20% of the carbon emitted from limestone during cement manufacture. This is much less than the 95% reduction initially promised by the project, suggesting that the technology still has some way to go before it makes a meaningful contribution.
Using less cement, or rather using less clinker, which is the component of cement responsible for the high emissions, is the other strategy to reduce emissions from concrete. One widely-used product is “fly ash”, which is a waste product of burning coal. This can be used to replace some of the clinker in cement. In the longer term, it’s not a solution, as we have to stop burning coal (I’ll be writing more on that soon). But while it is available, it’s better to use it in cement than dump it. Another addition is “slag”, which is waste created in blast furnaces during steel manufacture. Slag can replace a considerable proportion of the Portland cement in concretes, and concretes which contain it are often more durable. However, they are also slower to set, so have some disadvantages. There’s also a type of cement based on heated clay and unheated limestone, which requires lower temperatures than Portland cement and doesn’t release carbon dioxide during manufacture. Because it uses commonly available materials and a similar manufacturing process to Portland cement, it’s likely to be economically feasible.
Since 1990, the average proportion of clinker in cement has declined from 83% to 66%. This is an encouraging sign, but it is not clear how much lower it can go. Project Drawdown (a group which presents information on climate solutions) estimates that the proportion of clinker in cement could be from 46-61% by 2050.
Despite the relatively limited public attention, concrete is slowly reducing its carbon footprint. The Global Cement and Concrete Association has said it will reach net zero emissions by 2050. To do this, they will need to develop new technology for recapturing carbon. They are not using offsetting, that is, planting trees to try and make up for their emissions. This is a positive sign. But we also need to think about using less concrete.
There is research into concrete alternatives as well, for example, using wood. This is not just a case of going back to old methods and using ordinary timber, but using new wood products like cross-laminated timber. This product starts with natural timber but then processes it to give it greater strength and excellent fire-resistance. But you still have to ask careful questions about the origin of the wood. The last thing we need is more natural forest clear-felled to replace concrete.
This week, Bernard Hickey (who writes The Kaka) invited me to speak with him about methane and on his podcast “When the facts change”. You can listen to the episode here.
The Turnstone is free, but if you would like to support my work with a monthly or annual subscription, click the “Subscribe now” button below for options.
If you would like to support The Turnstone with a one-off contribution, click the “Buy me a coffee” button below.
So fascinating! Loved this deep contextual explanation. Your essays would be awesome as a collection for those trying to connect one issue with the gazillion others within the climate space.
Fascinating! I had no idea concrete was such a big CO2 producer...I like that you talked about some initiatives working to diminish its impact, as well. I remember touring a cement plant in my hometown...it is really an amazing process, mind-boggling to think of the Romans doing substantially similar work 1400 years ago.